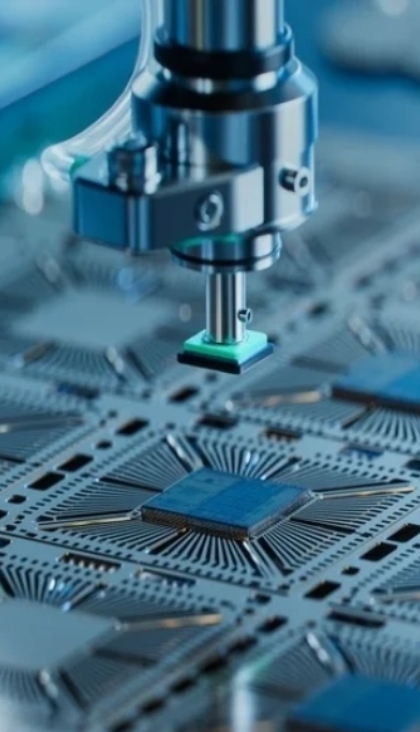
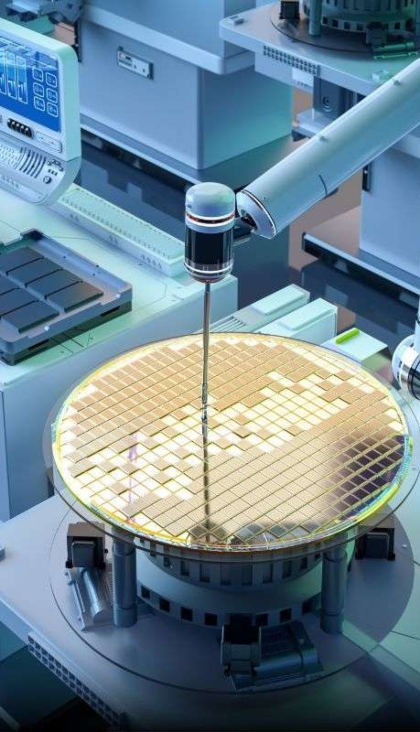
INDUSTRIES WE SERVE
Semiconductor
The semiconductor industry demands ultra-precise automation solutions to manage cleanroom environments, complex manufacturing processes, and strict quality control. We specialize in:
Cleanroom Environmental Control
Precise automation of temperature, humidity, and particle levels to maintain ISO-class cleanroom standards.
Advanced Process Automation
Integration of PLC, SCADA, and MES systems to control wafer fabrication, etching, doping, and inspection processes.
Equipment Integration & Monitoring
Seamless connection and monitoring of high-precision tools, ensuring real-time data collection and predictive maintenance.
Yield & Quality Optimization
Implementation of automated quality control and defect detection systems to enhance product yield and reduce waste.
Energy & Utility Management
Efficient control of critical utilities including gas delivery, vacuum systems, and deionized water for safe, stable operations.
KEY STRENGTHS
Smart Automation Solutions for Semiconductor Excellence
We deliver advanced automation systems tailored to the unique demands of semiconductor manufacturing. Our solutions enable precise environmental control, seamless system integration, and reliable performance to support cleanroom operations, high-throughput production, and continuous uptime. Designed for flexibility and scalability, our approach ensures consistent quality, operational efficiency, and long-term success in a rapidly evolving industry.
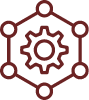
Precision Control for High-Purity Environments
Our automation systems are engineered for ultra-sensitive cleanroom environments, ensuring tight control over temperature, humidity, and airborne particles to maintain semiconductor-grade purity and process consistency.
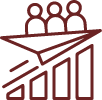
Seamless Integration Across Complex Systems
We specialize in integrating diverse equipment and subsystems—from fabrication tools to facility utilities—into unified platforms using PLC, SCADA and MES, enabling centralized monitoring and streamlined operations.
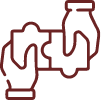
Reliability and Uptime Assurance
With built-in diagnostics, redundancy, and predictive maintenance features, our solutions are designed to maximize system availability and reduce the risk of downtime in high-throughput data semiconductor production lines.
OUR GOAL
Delivering Excellence Through
and Yield
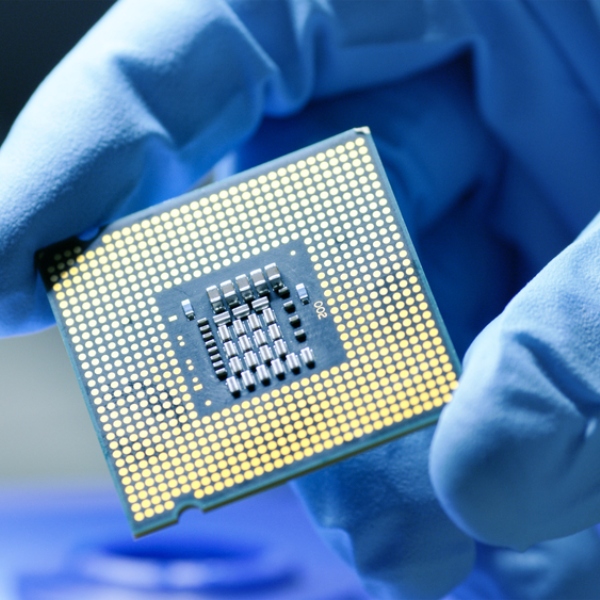
We develop detailed engineering documents including process flow diagrams, control narratives, and equipment specifications. Leveraging industry-standard software like EPLAN and AutoCAD, we ensure designs meet strict cleanroom and production standards.
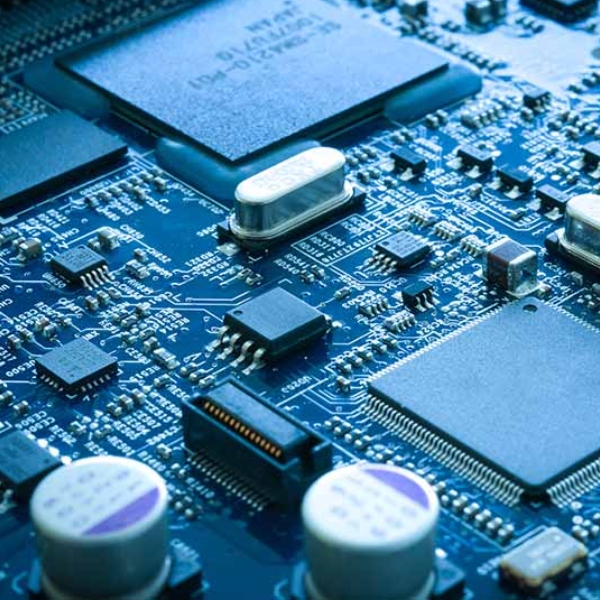
Our team configures and assembles control panels, instrumentation, and automation hardware with precision, following IEC and UL standards. Comprehensive in-house testing ensures system reliability before deployment.
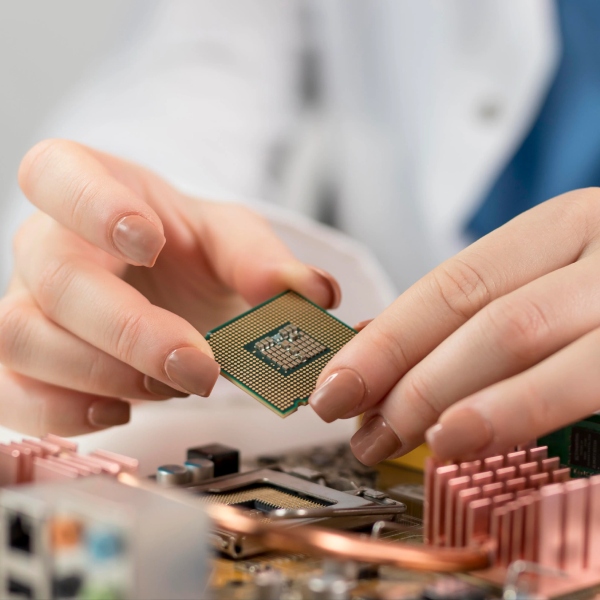
On-site installation is conducted with minimal disruption to production schedules. We perform thorough system validation, functional testing, and integration checks to ensure seamless operation within the semiconductor manufacturing environment.
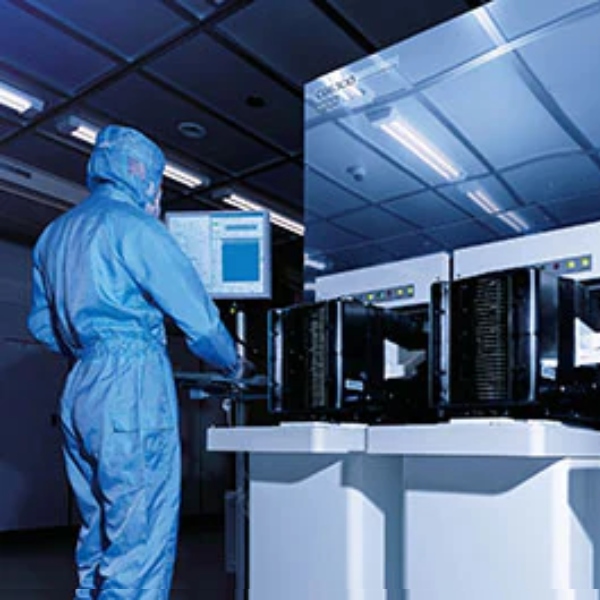
Post-installation, we provide continuous support including performance monitoring, troubleshooting, and system upgrades. Our proactive maintenance programs help optimize yield, reduce downtime, and adapt to evolving process needs.
project phases
Streamlined Project
Execution in Four
Phases
Reference List
Rubicon
Project:
FPSO Vantage
Details:
Emergency Shutdown System Fire and Gas Detection System Process Control System Process Shutdown System Allen-Bradley PLC in redundant configuration (Thailand)
Croda
Project:
Pilot Plant
Details:
Explosion Proof (Ex d and Ex e) Control Panels using Schneider PLC STAHL HMI and Wonderware SCADA (Singapore)
ECO Special
Waste Management
Project:
Control System for Incinerator 1
Details:
Schneider PLC communicating with Schneider VFDs across Ethernet and Wonderware НМІ (Singapore)
Rubicon
Project:
FPSO Front Puffin
Details:
ESD, PCS and FGS using DeltaV (Nigeria)
Croda
Project:
PLC Conversation
Details:
Conversion of Allen-Bradley PLC5 to Redundant ControlLogix (Singapore)
Dutch Incinerators
Project:
Udon Thani Medical Waste Incineration
Details:
Incineration Waste Incineration Plant using Schneider PLCs with Wonderware HMI (Thailand)
Mayekawa
Project:
Saudi Aramco
Details:
Flare Gas Recovery Compressor using Allen Bradley PLC (Kingdom of Saudi Arabia)
UMC
Project:
Slurry Distribution System
Details:
Control System for Slurry Distribution Machines using Redundant Allen- Bradley PLCs and Wonderware HMI (Singapore)