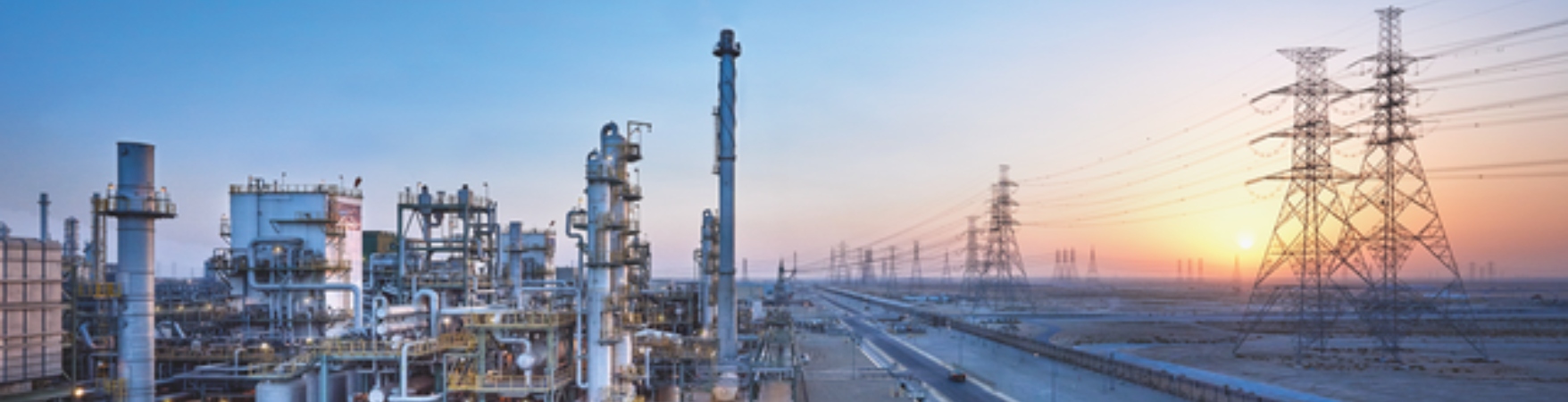
Supervise Workplace Safety and Health in Process Plant (SWSHPP, Formerly MOM OPISC)
Note: This is NOT the SCDF mandated CERT course. Please refer to our WSQ RFIW course if you require the CERT course that is regulated by SCDF.
- 32 hours
- English
- Centrium Square, Klane Lane
$165.00
(Subsidy for Citizen and PR)
Course Overview
The purpose of this SWSHPP competency unit is to enable learners to Supervise Workplace Safety and Health in a Process Plant.
On completion of this unit, learners will have the knowledge and application skills to carry out hazard identification and risk assessment, comply with the safety and health management system, co-ordinate a permit-to-work system, and carry out safety inspections and investigations.
Learning Units
- Identify and comply with legislation and regulations relevant to oil/petrochemical industry when carrying out the duties and responsibilities of a supervisor
- Perform the roles and responsibilities of the supervisors to ensure workplace safety and health
- Conduct job safety analysis for a job or task
- Identify safety and health hazards associated with the job or task
- Evaluate the level of risks involved in identified hazards
- Develop ways to eliminate/mitigate hazards identified in accordance with risk management regulations
- Co-ordinate measures to control risks according to the organisation’s procedures
- Complete a risk assessment form
- Communicate risks to stakeholders according to the organisation’s procedures
You Will Gain Competency In
- Identify and comply with legislation and regulations relevant to the oil/petrochemical industry when carrying out the duties and responsibilities of a supervisor:
- Importance: Compliance ensures that all operations are in line with established standards, thus reducing legal liabilities and potential fines. It helps in maintaining the license to operate and avoids disruptions caused by non-compliance.
- Perform the roles and responsibilities of the supervisors to ensure workplace safety and health:
- Importance: Supervisors are the frontline leaders who can directly influence worker behavior and safety culture. Their active participation and vigilance are crucial in preventing accidents, injuries, and fatalities.
- Conduct job safety analysis for a job or task:
- Importance: Job Safety Analysis (JSA) identifies potential hazards before they cause harm. It’s a proactive approach that ensures that workers understand the risks associated with specific tasks and take necessary precautions.
- Identify safety and health hazards associated with the job or task:
- Importance: Recognizing potential hazards is the first step in preventing accidents. By being aware of possible dangers, proactive measures can be taken to safeguard employees and assets.
- Evaluate the level of risks involved in identified hazards:
- Importance: Not all hazards are equally risky. Evaluating the risk level helps prioritize safety interventions and allocate resources where they’re most needed.
- Develop ways to eliminate/mitigate hazards identified in accordance with risk management regulations:
- Importance: Eliminating or mitigating risks ensures the safety of workers and reduces potential operational downtimes. This also aligns with regulatory requirements, showing a proactive approach to safety.
- Co-ordinate measures to control risks according to the organization’s procedures:
- Importance: Coordination ensures that risk control measures are effectively implemented across all sectors of the organization. This leads to consistency in safety practices and reduces chances of oversights or lapses.
- Complete a risk assessment form:
- Importance: Documentation provides a record of safety assessments, actions taken, and serves as evidence of due diligence. It can also be useful for future reference, training, and continual improvement.
- Communicate risks to stakeholders according to the organization’s procedures:
- Importance: Proper communication ensures that everyone involved, from workers to upper management, is informed about potential risks. This fosters a culture of safety where everyone is aligned and proactive about potential dangers.
Who Is This Course For?
The course would be appropriate for individuals who are contractors, managers and supervisors from the process industry.
Prerequisite
-
Workplace literacy and numeracy Level 5 under Employability Skills System (ESS)
Workplace Literacy and Numeracy Level 5 or equivalent. - ‘O’ level completed for Singaporeans
- Form 3 completed for Malaysians
- Secondary School Leaving Certificate (SSLC) for Indians
- Secondary School Certificate for Bangladeshi
Learn At AAT Training Hub!
Certification
Upon fulfilling the course requirements with a minimum attendance rate of 100% and demonstrating proficiency in the assessments, candidates will be awarded a
- Certificate of Completion from AAT Training Hub
- Nationally recognised WSQ Statement of Attainment
FAQs
Who is this course for?
The course would be appropriate for individuals who are contractors, managers and supervisors from the process industry.
What certificates will I receive upon completing the course?
- Certificate of Completion from AAT Training Hub
- WSQ Statement of Attainment
How do I register for the course?
Course Info
Categories: School of Safety Sciences
Lession: 1
Duration: 32 hours
Language: English
Location:
Centrium Square,
#10-03,Serangoon Road,S218108
(Located near Farrer Park MRT)Blk 672A Klang Lane, #01-97, Singapore 211672
Any queries?
Email Us: admin@aattraininghub.com
Whatsapp: +6590177049